TIG, MIG & Spot Welding
Service Metal Fabricators’ offers a wide range of customized precision sheet metal fabrication services, including TIG, MIG, and spot welding capabilities. Our highly trained welders can meet the unique specifications for a wide range of project requirements. Read further to learn more about our welding services:
Spot Welding for Precision Sheet Metal Fabrication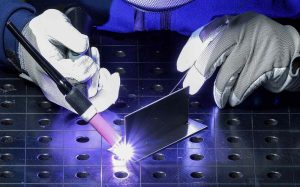
Spot welding, a type of resistance welding, is one of the precision welding techniques Service Metal offers our customers. This method of welding is primarily used for affixing larger metal surfaces together. This welding method is a precise, cost-effective process often used in lieu of riveting or stick welding techniques..
Precision Sheet Metal Fabrication: MIG Welding vs. Spot Welding
MIG welding, also known as metal inert gas welding, is a precision welding technique that can be used as an alternative to spot welding for sheet metal fabrication. Characterized by its use of solid wire electrodes and welding gun equipment, MIG welding is one of the most well-known and widely used forms of welding.
Precision Sheet Metal Welding: TIG Welding vs. Spot Welding
In addition to MIG welding and precision spot welding for sheet metal, SMF provides high-quality TIG welding services. This process, which is also known as GTAW welding, is better suited to Aluminum and produces more controlled, finer welds. TIG welding offers the highest level of precision for sheet metal enclosures.
Choosing between MIG, TIG and Spot Welding, Full Versus Stitch Welds, or Perhaps Even Riveting
Most of our metal enclosures and chassis require the highest attention to cosmetics, such that full TIG or MIG welding, followed by grinding, and dressing for paint/powder are necessary to essentially make the weld disappear entirely on the finished product. However, not all metalwork requires this meticulous attention to detail.
Service Metal has helped countless customers economize on the processes that add cost to their products and, therefore, saved them money. Sometimes this has led to Stitch welding solutions, most often on the inside of two joined metal surfaces. Stitch welding prescribes an agreed-upon interval of welded and non-welded spaces alternating along a seam. Applying this process inside can eliminate the need for grinding and lower weld time. Other times, an optimal solution can come from choosing the right rivet to join metal surfaces or sub-parts. SMF has the knowledge and experience to help advise, but only if your design specs remain open for such input. Otherwise, we stand ready to produce quality metalwork exactly to your specs.